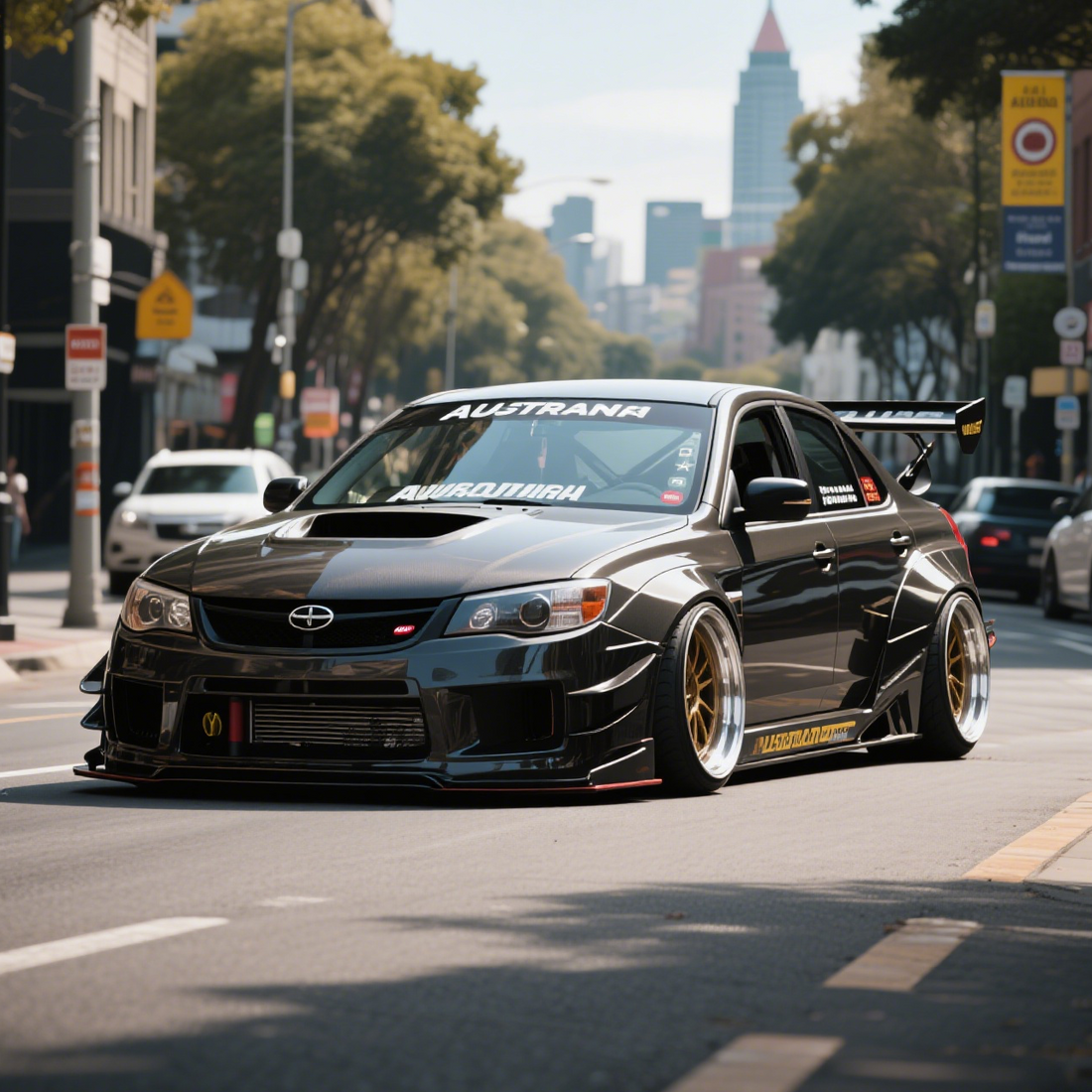
Titanium Wheel Bolts: Unsprung Mass Upgrade and Performance Revolution for Australian Car Owners (Real-World Data + Aumotor Localization Guide)
Share
Introduction
"While Sydney’s tuners battle for a 0.1-second advantage on the Eastern Creek racetrack, Melbourne’s Golf GTI is already speeding down the path of lightweight upgrades—and a tiny titanium wheel bolt might just be the ‘secret weapon’ in this race. Combining NASA-grade material data with Australian real-world case studies, this article reveals why titanium is revolutionizing the local modification market."
Titanium vs Steel: A ‘Dimensional Overkill’ in Strength
Titanium screws are about 60% lighter than steel screws, have almost the same strength as carbon steel and even exceed the latter's strength, and also have better corrosion and heat resistance. However, titanium is difficult to process and the cost is quite high. The main uses are shown below.
- Titanium alloy: High strength for the weight of the material, so it is used in aerospace-related products. Processing is very difficult, resulting in a higher unit price for screws.
The main steel materials used for screws are shown below.
- Carbon steel: the more common steel material for screws. Among them, S45C (carbon content of about 0.45%) is a hardness and strength of both mechanical structure of carbon steel materials, mostly used for screws.
- Alloy steel: With the addition of Mo (molybdenum) and Cr (chromium), it is used for bolts that require strength.
The decision to use titanium bolts largely hinges on weight reduction. The lightweight nature of these bolts optimizes unsprung mass and enhances driving dynamics. From our research, not only our brand but also Japanese and German alternatives have been praised by car enthusiasts in their shared experiences. At Aumotor, we are committed to providing Australian customers with premium-grade bolt fasteners. For instance, local Volkswagen Golf R and Golf GTI owners choose our titanium products for both superior aesthetics and performance gains.
What Are Sprung Mass and Unsprung Mass?
The weight of an automobile can be divided into two major parts, namely, the unsprung mass and the unsprung mass. The unsprung mass refers to the weight supported by the suspension system and the elastic elements, including the frame, the engine, the transmission, and the passengers, etc.; the unsprung mass refers to the parts that are not supported by the elastic elements of the suspension system, including, the wheels, the tires, the suspensions, the shock springs, the dampers, and other parts. It can also be simpler to understand unsprung mass as the parts that move with the suspension, while the parts that do not move with the suspension can be viewed as unsprung mass.
In reality, however, there are many parts of the body that are not very clearly defined as either unsprung or unsprung mass, such as half-shafts, shock springs, and other parts. They are attached to the body at one end, but at the other end they are attached to the suspension or wheels and move with the suspension. These parts are usually considered to be 50% unsprung mass and 50% unsprung mass.
Speed, Suspension Response, and Ride Comfort
-
Low-Speed Driving (e.g., 20 km/h over speed bumps):
The suspension has ample time to absorb impacts, reducing discomfort. -
High-Speed Driving (e.g., 80 km/h on rural highways):
Heavy unsprung mass causes delayed suspension adjustments, leading to harsh impacts.
Key Insight: Reducing unsprung mass (e.g., via titanium hub bolts) gives the suspension more time to react, even at higher speeds.
Suspension Design: Independent vs Torsion Beam
Design | Unsprung Mass Impact | Performance on Australian Roads |
---|---|---|
Independent Suspension | Lower unsprung mass, faster response to bumps | Smoother ride on Melbourne/Sydney urban roads |
Torsion Beam Axle | Higher unsprung mass, slower reaction to road shocks | Cost-effective but less comfortable |
Pro Tip: Pair lightweight components (e.g., titanium fasteners) with tuned dampers for maximum comfort on rough roads.
Why This Matters for Australian Drivers?
- Pothole Survival: Lower unsprung mass (e.g., alloy wheels) reduces shock loads on suspensions, cutting repair costs—critical for cities like Brisbane and Perth.
- Off-Road Advantage: Lightweight suspensions improve tire grip on unsealed outback tracks.
-
Fuel Efficiency: Reduced inertia from lightweight parts slightly improves fuel economy—key for long-distance travel.
As defined by Dr. Chris Hilton
As a fastener of the wheel, the mass of the bolt is not carried by the suspension. The original bolts of the car are produced according to a uniform standard, the core criteria of which are the tensile and yield strengths, i.e., safety, to ensure the carrier's roadworthiness. Modified parts, on the other hand, pursue higher performance, lighter mass, and more diverse designs on the standard of safety. Titanium alloy wheel bolt is considered a popular option among the modified bolt options that Aumotor offers to its customers.
In addition, according to the physical equation: rotational kinetic energy = ½ x moment of inertia x angular velocity². Titanium screws reduce wheel rotational inertia due to their lighter weight.
Technical Comparison Table
Trait | Aumotor Ti-6Al-4V Titanium | Standard Steel Bolts |
---|---|---|
Tensile Strength | ≥1110 MPa | Grade 5: ~825 MPa Grade 8: ~1035 MPa |
Yield Strength | 830–900 MPa | Grade 5: ~635 MPa Grade 8: ~895 MPa |
Fatigue Strength (10⁷ cycles) | 500–600 MPa | Grade 8: 300–400 MPa |
Corrosion Resistance | Superior (No coating needed) | Requires coating (e.g., zinc) |
High-Temperature Performance | Stable up to 400°C | Strength drops sharply above 250°C |
Specific Strength (Strength/Density) | 203–226 MPa·cm³/g | Grade 8: ~132 MPa·cm³/g |
Typical Applications | Racing, Aerospace, Premium Vehicles | Daily Drivers, Commercial Trucks |
Key Takeaways for Australian Drivers
-
Red Dirt Dominance:
Aumotor’s titanium bolts resist corrosion from Australia’s salty coastal air and acidic red soil. -
Heat Resistance:
Maintain strength in extreme conditions (e.g., Outback summers or heavy towing), where steel bolts weaken. -
Fatigue Life:
With double the fatigue strength of Grade 8 steel, Aumotor bolts survive relentless corrugations on roads like the Gibb River Road. -
Weight Savings:
Titanium’s unmatched specific strength reduces unsprung mass, improving suspension response on rough tracks.
(Generated by ai)
Why is unsprung quality so important to Australian car owners?
- Bumps and Unpaved Roads: The outback, country roads and some city streets (e.g. Hoddle Street in Melbourne, Parramatta Road in Sydney) have a lot of potholes, gravel roads and cracks. The high unsprung mass amplifies the impact forces, causing the suspension to be subjected to frequent and severe vibrations, accelerating component wear.
- Off-Road Needs: Many vehicle owners drive four-wheel drive vehicles or SUVs on off-road adventures. In rough terrain, lightweight under-sprung components enhance tire adhesion, reduce bouncing and improve handling safety.
- High temperatures and corrosion: The high salt air in coastal areas accelerates rust and corrosion of metal parts. Lightweight materials such as titanium alloys are highly resistant to corrosion, making them suitable for the Australian environment.
- Maintenance costs: remote areas are difficult to repair, lowering the unsprung mass reduces the frequency of failures, saving time and money.
- The value of lightweight bolts: Using Ti-6Al-4V titanium alloy bolts instead of steel bolts reduces unsprung mass and directly reduces the load on the suspension system. This optimization extends shock absorber life and improves ride smoothness over potholes in Australia's bumpy road conditions.
- Industry Practice: The Australian tuning market widely promotes lightweight wheels and aluminum alloy suspension components, which confirms the importance of unsprung mass to vehicle owners.
Aumotor provides titanium alloy bolts and nuts, which are suitable for more than 95% of the models in the Australian market, covering the classic BBA models and the electric models currently on the market, and the Pickup, which is the choice of 60% of the car owners in Australia, is also suitable, and the length of the bolts is provided with customized service to meet the adaptive needs of wheel spacers for some of the vehicles.
(Generated by ai)
Aumotor Installation Guide
Torque value setting:
Family car: 90-110Nm (refer to Toyota manual)
Performance cars: 110-130Nm
WARNING: Do not use values greater than the above for installation resulting in cracked wheels and other safety hazards.
Required Tools:
Non-slip sleeve (free with purchase)
Local brand “Torque Masters” wrench (available at Bunnings)
Controversy and Truth: 5 Myths About Titanium Screws
“Titanium alloy is weaker than aluminum?”
Fact: Titanium alloys have 3 times the tensile strength of 6061 aluminum alloys (900MPa vs 310MPa) and better fatigue resistance.
“Only luxury cars need it?”
Every owner has the right to customize their vehicle when it is safe to do so, and we offer the same grade 12.9 steel bolts and nuts in aluminum alloy housings.
“The anodized color will come off?”
The titanium material is inherently resistant to oxidation and corrosion, there is no need to worry about high pressure water gun rinsing or salt spray, the exterior color is permanent.
“How about just replacing the lightweight wheels?”
Every kit is necessary on the way to lightweighting, and since you're going for the driving experience, you have to follow through.
“Is it allowed by Australian law?”
Compliance: Aumotor's titanium products have been tested for destruction by tensile strength, proof load, yield strength, hardness, Over 10 TÜV Reports Certified, Reliable Quality Guarantee.